Slip trailing pottery is a versatile liquid mixture of clay and water that serves various purposes in ceramics, from joining pieces to creating decorative effects. Whether you’re a seasoned potter or a beginner, learning how to make pottery slip is an essential skill in crafting pottery. It is easy to prepare and can be customized depending on its intended use, making it an invaluable tool in the art of ceramics.
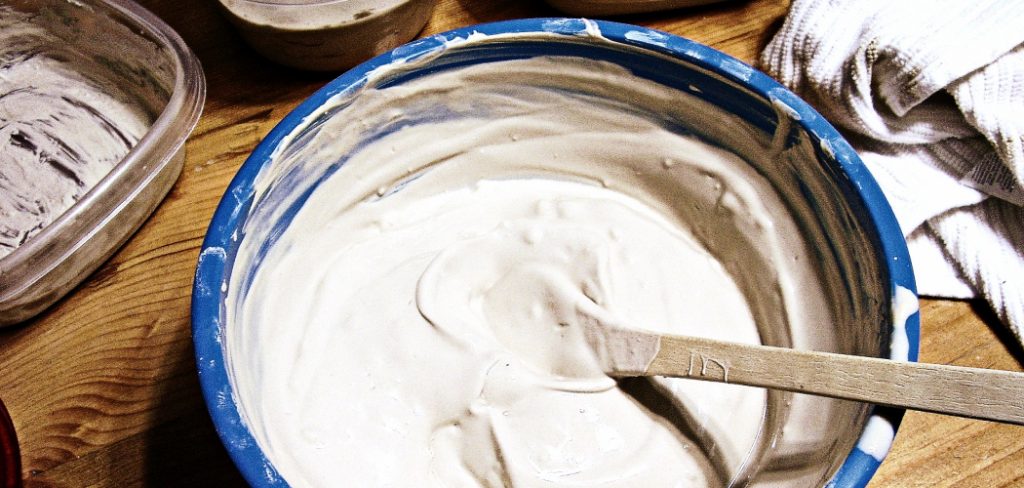
The Role of Slip in Pottery and Ceramics
Slip plays a fundamental role in both functional and decorative aspects of pottery and ceramics. It is commonly used as an adhesive to join clay pieces together, such as handles and embellishments, ensuring a strong bond when the clay is in its wet or leather-hard stage. Beyond its practical applications, slip is widely appreciated for its creative potential in decorating finished pieces.
By applying slip with brushes, sponges, or slip-trailing tools, potters can create intricate patterns, textures, and color contrasts on the surface of their work. Additionally, slip can be used in techniques like slip casting, where liquid clay is poured into molds to form precise, repeatable shapes. Its versatility makes it an indispensable material for both traditional and contemporary pottery practices.
Understanding Pottery Slip
Pottery slip is essentially liquid clay, created by blending clay with water until it achieves a smooth, paint-like consistency. The ratio of clay to water can vary depending on the desired thickness and purpose of the slip. For instance, thicker slips are often used in slip trailing and decorative techniques, while thinner slips are ideal for slip casting.
The quality of the clay used, as well as the addition of other materials like deflocculants or colorants, can significantly influence the properties of the slip. Deflocculants, such as sodium silicate, help to keep the clay particles suspended in water and reduce the overall water content required, making the slip more fluid while maintaining a high clay concentration. Understanding these elements is crucial for controlling the behavior of the slip and achieving the desired results in your pottery projects.
Gathering Your Materials
To create pottery slip, you’ll need a few basic materials and tools, most of which are readily available in a pottery studio or craft store. Start with a clay body of your choice, as the slip should ideally match the clay used in your project to ensure compatibility during firing. You’ll also need water, preferably clean and free of impurities, to help achieve the right consistency.
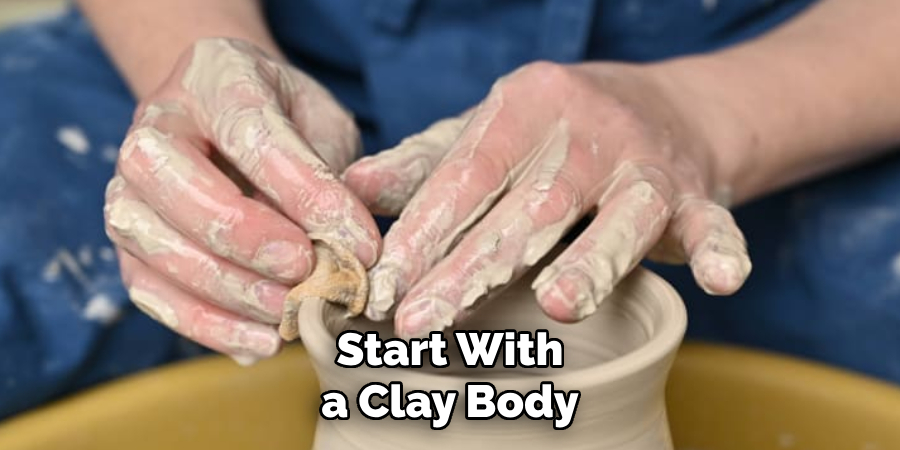
For more advanced techniques, consider having deflocculants like sodium silicate or Darvan on hand, which can enhance the slip’s fluidity without excessive water. If you plan to add decorative elements, powdered oxides or stains can be included to color the slip. Lastly, gather tools like a bucket or container for mixing, a spatula or mixing stick, and a sieve to create a smooth, lump-free mixture. Having all these materials prepared beforehand will make the process of creating pottery slip efficient and successful.
10 Methods How to Make Pottery Slip
1. Traditional Clay and Water Slip
One of the simplest ways to make pottery slip is by mixing dry clay with water until it reaches a smooth, creamy consistency. Start by breaking down dry clay into small pieces and gradually add water while stirring. Allow the mixture to sit overnight to fully absorb the water. Blend the mixture using a hand mixer or a drill with a mixing attachment to remove lumps and ensure uniformity. This basic slip is ideal for joining clay pieces and coating surfaces.
2. Reclaiming Clay Scraps for Slip
Recycling clay scraps is an efficient way to make slip while reducing waste. Collect leftover clay pieces from trimming or failed projects and allow them to dry completely. Once dried, crush the clay into small bits and submerge them in water for several hours. Stir periodically to help break down the particles. After the clay fully absorbs the water, blend the mixture until it reaches a smooth, pourable consistency. This method is perfect for conserving resources and creating a sustainable pottery practice.
3. Deflocculated Slip for Casting
A deflocculated slip is used for slip casting, where liquid clay is poured into plaster molds. This type of slip requires the addition of a deflocculant, such as sodium silicate or Darvan, which helps reduce water content while maintaining fluidity. To prepare, mix dry clay with water, then slowly add the deflocculant, stirring continuously. Use a viscosity cup to ensure the right consistency. This method is excellent for producing uniform and detailed ceramic forms with molds.
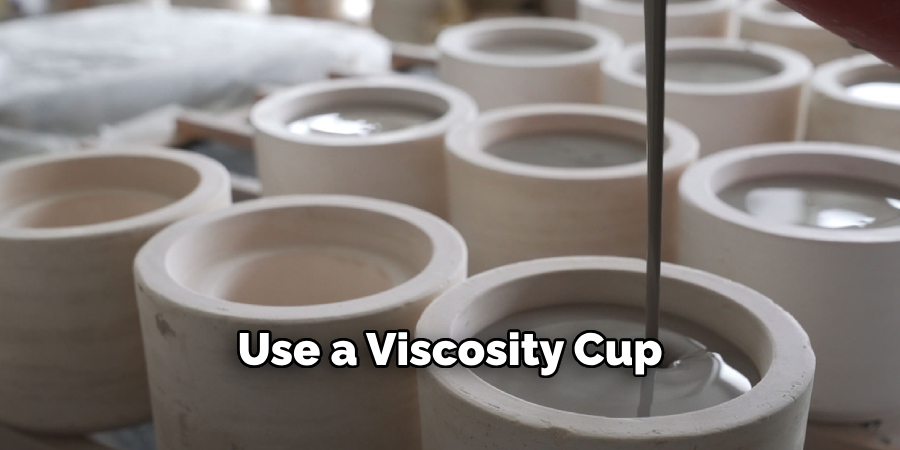
4. Engobe Slip for Surface Decoration
Engobe is a specialized slip that contains added colorants and is used for decorating pottery. To make engobe, mix a fine clay body with water, then incorporate oxides, stains, or pigments to achieve the desired hue. Ensure the mixture is well blended using a blender or sieve to avoid inconsistencies. Apply engobe to greenware or bisque-fired pieces for decorative effects such as sgraffito, painting, or trailing. This technique allows for vibrant and textured surface embellishments.
5. Terra Sigillata for a Polished Finish
Terra sigillata is an ultra-refined slip that creates a smooth, polished surface when applied to pottery. To make it, mix fine clay particles with water and a deflocculant, then let the mixture settle for 24 hours. The top layer, which contains the finest clay particles, is carefully siphoned off, leaving behind heavier sediment. This refined slip is applied in thin layers and burnished to produce a glossy, almost glass-like finish without glaze. It is commonly used in ancient pottery techniques and decorative ceramics.
6. Slip from Commercial Clay Bodies
For potters who use commercial clay bodies, making slip is straightforward. Simply take a portion of the wet clay and mix it with water until it reaches the desired consistency. To enhance fluidity, a small amount of sodium silicate or Darvan can be added. This method ensures that the slip matches the parent clay body, reducing issues of shrinkage or cracking when applied to pottery pieces.
7. Colored Slip for Artistic Expression
Colored slip allows artists to add vibrant designs to their pottery. Begin by making a base slip using any of the above methods. Then, incorporate ceramic stains, oxides, or natural pigments into the slip and mix thoroughly. For even distribution, blend the colored slip with a hand mixer or pass it through a fine mesh sieve. This method is widely used in slip trailing, stenciling, and painting on clay surfaces.
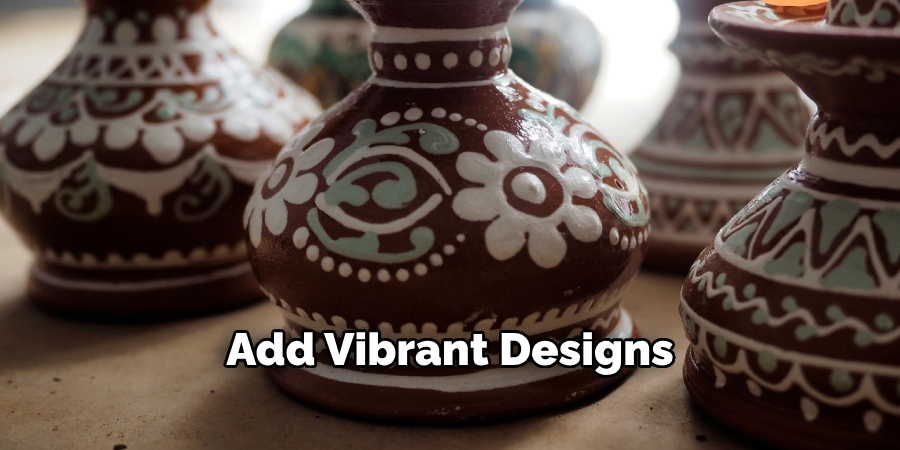
8. Paper Clay Slip for Strength and Flexibility
Paper clay slip is enhanced with cellulose fibers, making it stronger and more flexible. To prepare, mix shredded toilet paper or paper pulp with water and blend until smooth. Combine the paper pulp with clay slip and mix thoroughly. This type of slip is beneficial for repairing cracks, joining dry clay pieces, or creating lightweight ceramic sculptures. The added fibers help reinforce the structure, reducing the risk of warping or cracking during drying.
9. Salt Slip for Unique Surface Effects
A salt slip introduces sodium chloride into the clay mixture, creating unique textures and glaze-like effects when fired at high temperatures. To make it, mix a standard slip and add a small percentage of salt, ensuring it dissolves completely. When applied to pottery, the salt interacts with the kiln atmosphere, producing unpredictable and often stunning surface variations. This technique is frequently used in atmospheric firing methods, such as wood or soda firing.
10. Ash Slip for Natural Glazing
Ash slip incorporates wood ash into the slip mixture to create a natural glaze effect when fired. To make it, sift wood ash to remove large particles, then mix it with clay slip. Apply the ash slip to pottery and fire it in a kiln, allowing the ash to melt and form a glossy surface. This method has been used for centuries in traditional pottery-making, particularly in Asian ceramics, to achieve organic and dynamic finishes.
Maintenance and Upkeep
Proper maintenance of your slip and related tools ensures consistent results and prolongs the life of your materials. Store slip in airtight containers to prevent it from drying out or developing mold. If mold appears, mixing the slip thoroughly or adding a few drops of disinfectant, such as bleach, can help eliminate it without affecting the slip’s quality. Regularly stir or shake stored slip to maintain an even consistency. Clean all tools, containers, and equipment immediately after use to prevent dried slip from hardening and becoming difficult to remove. Additionally, ensure that water and clay residue are disposed of responsibly, avoiding sink drains to prevent clogs. Adopting these maintenance habits will support an efficient and sustainable pottery practice.
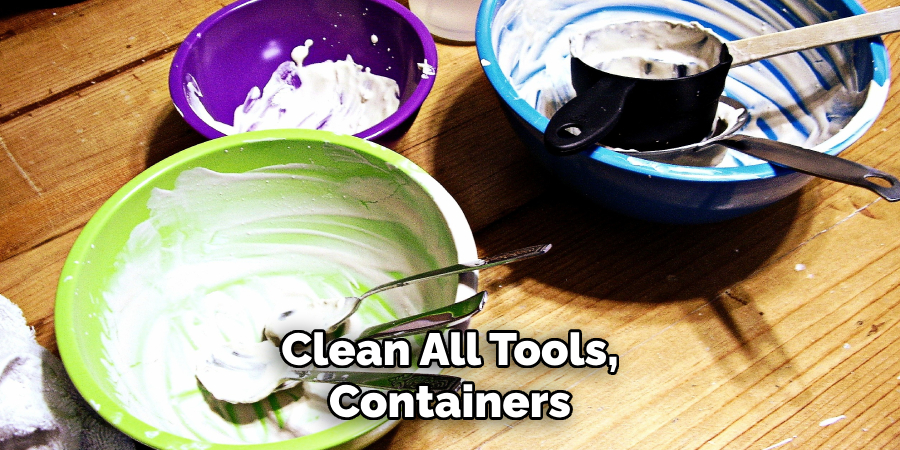
Conclusion
Making pottery slip is an essential skill for ceramic artists, offering numerous applications in decorating, casting, and joining clay pieces. By experimenting with different slip recipes, potters can achieve a variety of effects, from polished surfaces to textured finishes. Whether using reclaimed clay, adding colorants, or incorporating natural elements, each method provides unique advantages that enhance the creative process. So, there you have it – a quick and easy guide on how to make pottery slip.
Professional Focus
Toby Rede, a professional potter, combines artistic expression with functionality in his ceramic creations. His work blends natural textures, modern forms, and sustainable materials, making him a standout voice in the pottery world focused on intentional craftsmanship.
About the Author
Toby Rede, a dedicated potter and blogger, shares his insights on functional and artistic ceramics, drawing inspiration from sustainable gardening and nature. Based in his studio, he blends craftsmanship with everyday life, encouraging others to incorporate handmade pottery into their homes for both beauty and utility.
Education History
University: Alfred University
Degree: Associate Degree in Ceramic Technology
Toby’s education laid the foundation for his technical expertise, equipping him with the skills necessary to create pottery that merges functionality and aesthetic appeal.
Expertise:
- Pottery Creation
- Ceramic Techniques (Texture, Glazing, Sustainable Materials)
- Functional Art and Design
- Craftsmanship Philosophy
- Blogging on Handmade Pottery and Everyday Life