Creating ceramic butcher trays is a rewarding process that blends creativity with practicality. These trays are not only useful for organizing kitchen ingredients or art supplies but also offer a durable and aesthetically pleasing addition to any home. Whether you are a seasoned ceramist or a beginner looking to explore pottery, making ceramic butcher trays can be a fulfilling project.
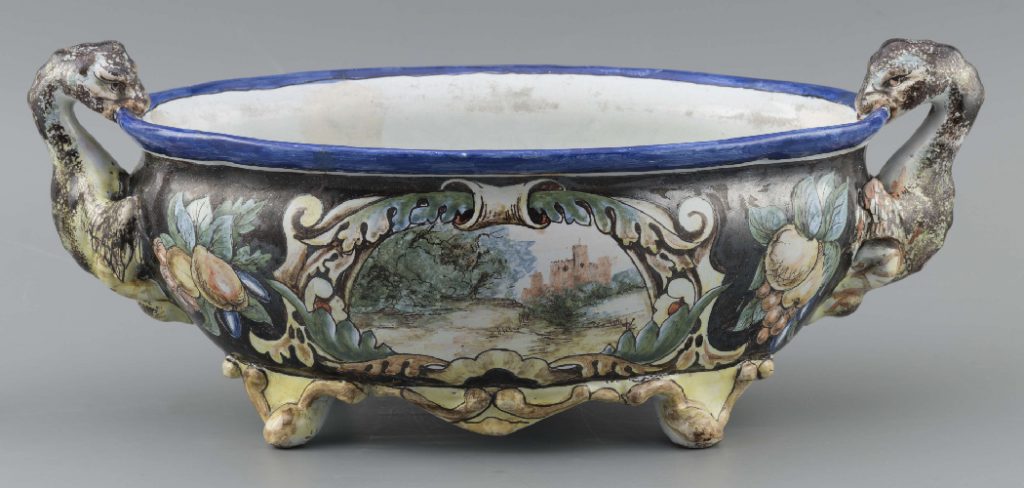
This guide on how to make ceramic butcher trays will walk you through the essential steps and techniques needed to craft your own trays, from selecting the right clay to achieving that perfect glaze finish.
Why Choose Ceramic?
Before we dive into the process of making ceramic butcher trays, it’s important to understand why this material is an excellent choice for this project. Ceramic is a versatile and durable material that can withstand high temperatures, making it ideal for use in kitchens or other areas where heat or moisture may be present. It also offers a smooth surface that is easy to clean and maintain, making it perfect for food-related items such as butcher trays.
It’s also worth noting that ceramic comes in a wide variety of colors and finishes, giving you the freedom to customize your butcher trays to match your personal style and preferences. Plus, with proper care, ceramic can last for generations, making it a sustainable and environmentally friendly option.
Materials Needed
To get started on your ceramic butcher tray project, you will need the following materials:
Clay:
Selecting the right type of clay is crucial to creating a successful butcher tray. Stoneware clay is recommended due to its durability and ability to withstand high temperatures. It also offers a smooth finish that is perfect for food-related items.
Clay Tools:
You will need various clay tools such as a rolling pin, cutting tool, and smoothing tool to shape and mold the clay into your desired tray form.
Kiln:
A kiln is necessary for firing or baking your ceramic trays at high temperatures to harden the clay and achieve a durable finish.
Glaze:
Glaze is what gives your ceramic butcher trays its color and glossy finish. You can choose from a variety of glazes depending on the look you want to achieve. Keep in mind that not all glazes are food safe, so be sure to select one that is specifically labeled as such.
Paintbrushes:
Paintbrushes are necessary for applying the glaze onto your trays. It’s recommended to use softer, natural hair brushes for a smooth and even application.
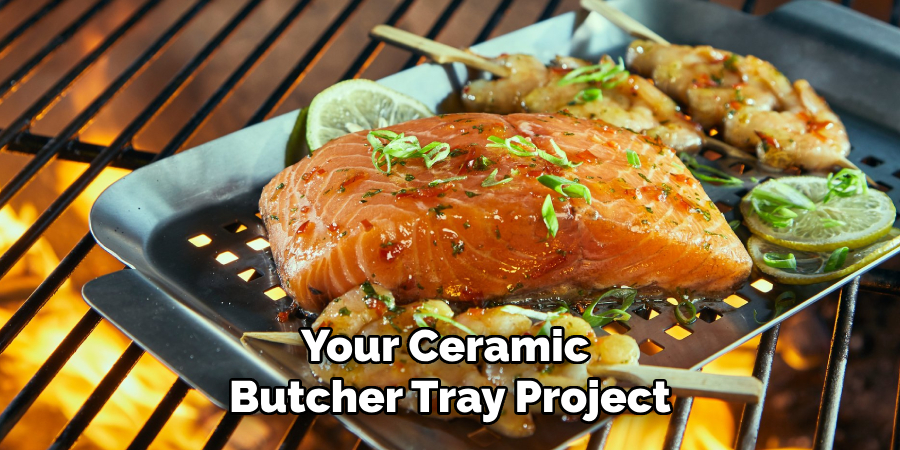
9 Step-by-step Guidelines on How to Make Ceramic Butcher Trays
Step 1: Begin by Preparing Your Clay
Start by wedging your stoneware clay to remove air bubbles and ensure a consistent texture throughout. This process involves kneading the clay much like dough pushing and folding it to make it more pliable and homogenous.
Once the clay feels smooth and uniform, roll it out on a clean and lightly floured surface using a rolling pin. Aim for an even thickness, ideally around 1/4 inch, to provide stability for the tray while also allowing it to dry and fire properly. By taking care of this foundational step, you’ll set the stage for a successful crafting process, reducing the risk of cracks or imperfections in the final product.
Step 2: Cut Your Clay into a Rectangle
Once you have rolled out your clay to the desired thickness, the next step is to cut it into a rectangle, which will form the base shape of your butcher tray. Using a straightedge or a ruler, measure out the dimensions you want for your tray. A typical size might be around 12 inches by 8 inches, but feel free to adjust according to your needs.
Use a cutting tool, such as a clay knife or a needle tool, to carefully slice along the lines you’ve measured, ensuring clean and straight edges. Take your time with this step to maintain precision, as the accuracy of these cuts will affect the overall symmetry and appearance of your finished tray. Smooth out any rough edges with a smoothing tool or a damp sponge to prepare the cut clay for the next steps in the process.
Step 3: Shape the Sides of Your Tray
Once you have your rectangular base, it’s time to add depth and shape to your butcher tray by creating raised sides. To do this, roll out two long, thin strips of clay that are about the same length as two opposing sides of your base. Make sure they are slightly taller than the thickness of your base to allow for shrinkage during firing.
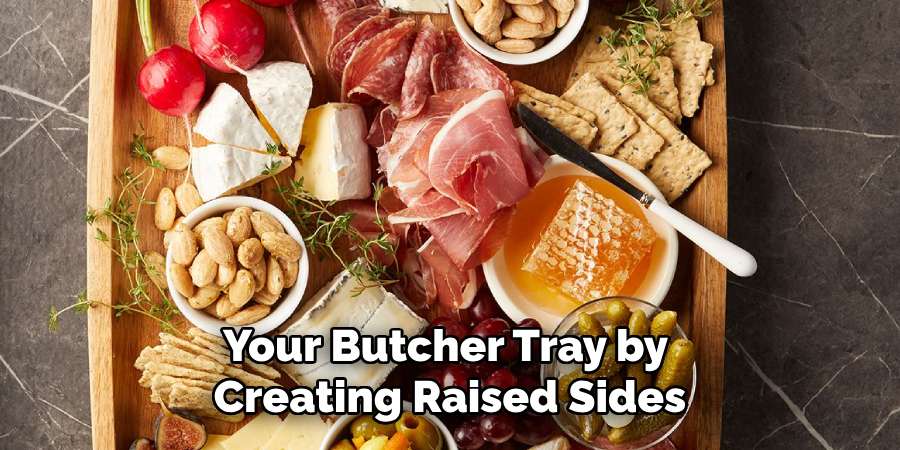
Next, place these strips onto the edges of your rectangle and use a smoothing tool or your fingers to attach them securely. This step may take some practice to get right, but don’t worry if the sides aren’t perfect even at this stage – you can always smooth and reshape them later.
Step 4: Smooth and Blend the Seams
Once your sides are attached, use a damp sponge or your fingers to smooth out any visible seams between the base and the added clay strips. This will help create a seamless transition between the two parts of your tray.
Use gentle pressure and circular motions to blend the clay together evenly, taking care not to distort or flatten the edges of your tray.
Step 5: Add Handles (Optional)
If you would like handles on your butcher tray, now is the time to add them. You can shape these out of extra pieces of clay by rolling them into thin ropes and attaching them where desired on the sides of your tray. Make sure to smooth and blend them seamlessly into the sides of your tray for a cohesive look.
Otherwise, you can skip this step and add handles later using glaze or other decorative elements.
Step 6: Dry Your Tray
Once your tray is fully formed and shaped, it’s time to let it dry completely. This process can take anywhere from a few days to a week, depending on factors such as humidity levels and the thickness of your clay. It’s important to allow the tray to dry slowly to prevent cracks or warping.
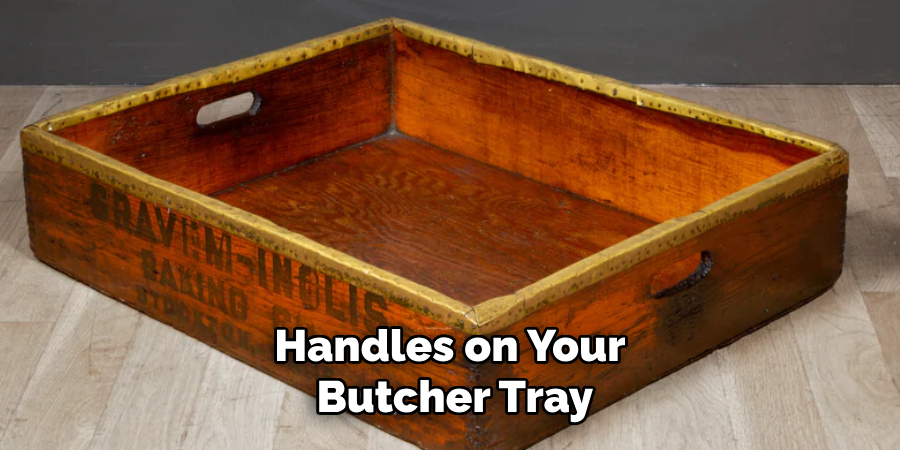
Place the tray on a flat surface in a well-ventilated area, turning it occasionally to ensure even drying. You can also place paper towels or cloths underneath the corners of your tray if they start to droop or bend while drying.
Step 7: Fire Your Tray in the Kiln
Once your tray is fully dry, it’s time to fire it in a kiln. This process will harden the clay and transform it into durable ceramic.
It’s recommended to follow the instructions provided by your specific kiln for temperature and firing times. Generally, you’ll want to start at a low temperature (around 1800 degrees Fahrenheit) and gradually increase over several hours until reaching a final temperature of around 2200 degrees Fahrenheit. Allow the tray to cool down completely before removing it from the kiln.
Step 8: Apply Glaze
Once your tray has been fired and cooled, it’s time to add color and shine by applying glaze. Use your preferred paintbrushes to carefully apply the glaze onto the tray, taking care not to overlap or create drips.
Follow the manufacturer’s instructions for drying and firing times for your specific glaze, as they may vary. Some glazes may require multiple coats for a richer color, so be sure to plan accordingly.
Step 9: Final Firing
Once you have applied the glaze and allowed it to dry completely, it’s time for a final firing in the kiln. This step is crucial for sealing and setting the glaze onto your tray.
Again, follow your kiln’s instructions for temperature and firing times, typically similar to those used for the initial firing. Once your tray has cooled, it’s ready to be used and displayed proudly in your kitchen or as a unique gift for friends and family.
Following these steps on how to make ceramic butcher trays and taking care along the way will result in a beautifully crafted butcher tray that is not only functional but also a work of art. With practice, you can even experiment with different shapes, sizes, and designs to create your own personalized versions. Happy crafting!
Frequently Asked Questions
Q: Can I Use Any Type of Clay for Making a Butcher Tray?
A: Yes, you can use any type of air-dry or kiln-fired clay to make a butcher tray. However, clay with a higher firing temperature and lower shrinkage rate may be more suitable for functional trays.
Q: Can I Make a Butcher Tray Without a Kiln?
A: Yes, you can make a butcher tray using air-dry clay and skip the kiln-firing process. However, keep in mind that air-dry clay may not be as durable and may require additional sealants or coatings for functionality.
Q: How Do I Care for and Clean My Butcher Tray?
A: To care for your butcher tray, simply wipe it down with a damp cloth after each use. Avoid soaking or submerging in water as this may cause damage to the clay or glaze. If needed, you can also gently scrub with mild soap and warm water, then dry thoroughly before use.
Q: Can I Customize My Butcher Tray with Different Designs or Colors?
A: Yes, you can customize your butcher tray with various designs and colors by using different types of clay, glazes, and techniques such as carving or painting. Get creative and make your butcher tray truly unique!
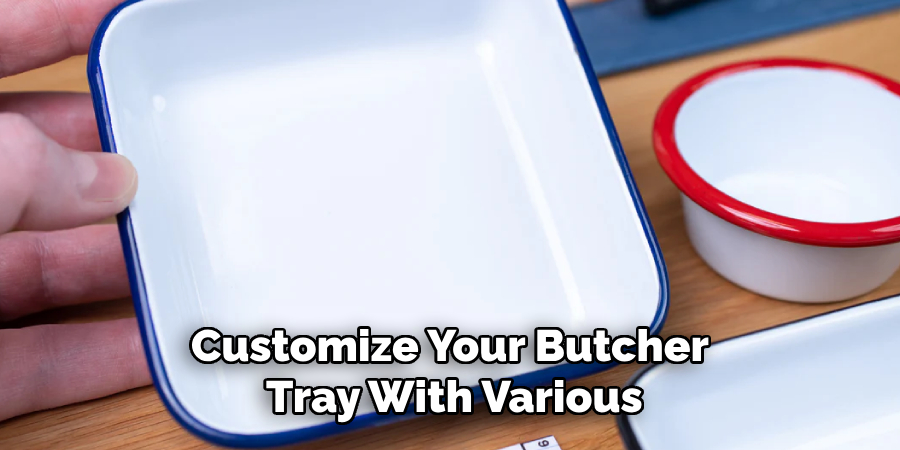
Conclusion
Creating your own ceramic butcher tray can be a rewarding and artistic endeavor, providing both a functional kitchen accessory and a personal expression of creativity. By carefully following each step on how to make ceramic butcher trays—from forming the base and shaping the sides to glazing and firing—you can craft a piece that reflects your style and craftsmanship.
Experimenting with different clays, glazes, and designs allows for endless possibilities, turning a simple project into a unique piece of art. Whether you’re making the tray for personal use or as a thoughtful gift, the effort you invest will cause errors to occur over generations. Please try again or contact support if it continues.
Professional Focus
Harry Ciotti is a highly skilled kiln operator with a sharp eye for detail and an in-depth understanding of the firing process. His expertise ensures that each ceramic piece reaches its full potential, perfectly balancing strength and beauty. Harry takes pride in overseeing the final stage of pottery creation, transforming raw clay into durable and stunning works of art.
About the Author
Harry Ciotti is a dedicated kiln operator and ceramic artist who brings passion and precision to every piece he fires. With a deep commitment to craftsmanship, Harry ensures that every ceramic creation is fired to perfection, from delicate vases to robust sculptures. He not only operates the kiln, but understands the unique needs of each piece, ensuring it reaches its full artistic potential. Through his work, Harry blends precision with artistry, making every firing a story of transformation.
Education History
University: California College of the Arts
Degree: Master of Fine Arts in Ceramics
Harry’s advanced education in ceramics has refined his technical skills, particularly in kiln operation, firing processes, and ceramic artistry. His educational background equips him to produce top-quality ceramic pieces that reflect both technical excellence and artistic expression.
Expertise:
- Kiln Operation and Firing Techniques
- Ceramics Creation (Functional and Artistic)
- Precision Craftsmanship
- Glazing and Texture Techniques
- Ceramic Artistry and Storytelling