Crafting ceramic brush holders is a delightful and rewarding process that combines creativity with functionality. Whether you’re an experienced ceramicist or a beginner looking to explore the art of pottery, making your own brush holder adds a personal touch to your workspace.
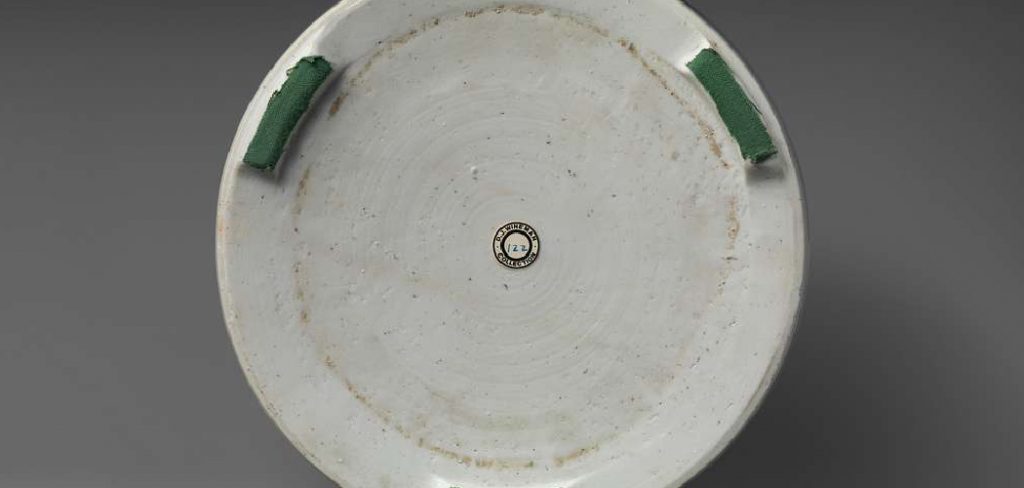
This guide on how to make ceramic brush holders will walk you through the steps to create a beautifully designed holder to organize your brushes, add aesthetic appeal to your space, and reflect your unique style. With just a few materials and some patience, you’ll be able to produce a piece that not only serves a practical purpose but also showcases your artistry.
Why Make Ceramic Brush Holders?
Ceramic brush holders offer a number of benefits that make them a popular choice among artists and crafters. Here are some reasons why you should consider making your own:
Customization:
By making your own ceramic brush holder, you have the freedom to choose the colors, designs, and patterns that best reflect your personality and artistic style. This allows you to create a one-of-a-kind piece that truly stands out and adds a personal touch to your workspace.
Durability:
Ceramic is a durable material, making it ideal for holding heavy and fragile brushes. Unlike plastic or metal holders, ceramic brush holders are less likely to break or crack over time, ensuring that your brushes will be well-protected.
Aesthetics:
A handmade ceramic brush holder not only serves as a functional tool but also doubles as a visually appealing art piece. With its unique design and handcrafted details, it can add a touch of elegance and charm to any room.
Materials You’ll Need
Before getting started, gather the following materials:
Ceramic Clay :
Choose a type of clay that is suitable for pottery and can withstand high temperatures without cracking. You can also opt for air-dry clay if you do not have access to a kiln.
Pottery Tools :
You will need basic pottery tools such as a knife, loop tool, sponge, and wire cutter to shape and sculpt the clay.
Rolling Pin or Slab Roller :
A rolling pin or slab roller will help you flatten the clay into even sheets, which will be used to create your brush holder.
Kiln:
If using ceramic clay, access to a kiln is necessary for firing the piece and making it durable. If using air-dry clay, no firing is required.
Glazes:
Choose glazes in your desired colors to decorate and add a glossy finish to your brush holder.
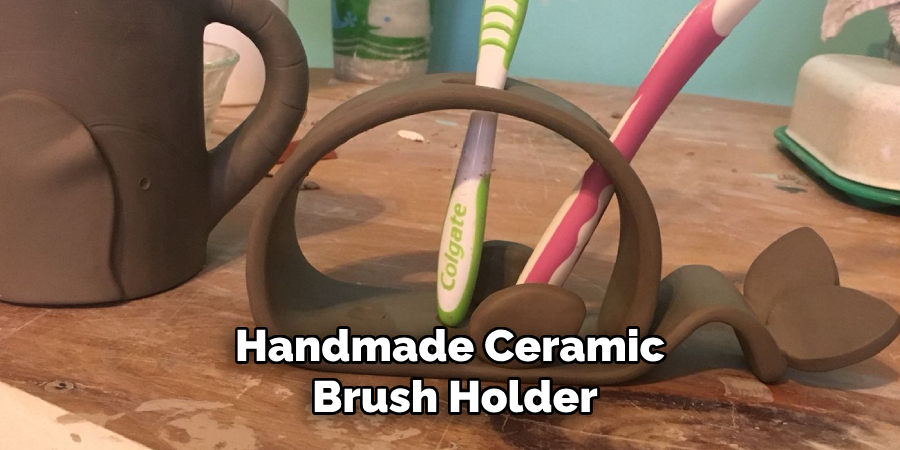
8 Step-by-step Guides on How to Make Ceramic Brush Holders
Step 1: Prepare Your Work Surface
Begin by setting up a clean and organized workspace to ensure a smooth crafting process. Cover your work surface with a cloth or plastic sheet to protect it from clay residue and spills. Ensure you have ample space to maneuver your tools and clay comfortably.
Arrange all necessary materials within easy reach, including your clay, tools, and any reference sketches or designs you plan to use. Proper preparation of your work area not only aids in maintaining cleanliness but also enhances your focus and creativity during the crafting process.
Step 2: Knead and Prepare the Clay
Knead the clay to remove any air bubbles and make it pliable. Working with a small amount of clay at a time, roll it into a ball on your work surface.
Using a rolling pin or slab roller, flatten the clay into an even sheet about ¼ inch thick. Continue to knead, roll, and flatten until you have enough sheets to create your desired brush holder size.
Step 3: Cut Out Your Design
Once you have rolled out the clay into an even slab, use a knife or a pottery cutting tool to carefully cut out the shapes that will form your brush holder. Typically, you will need a rectangular or cylindrical piece for the body, and you can cut additional shapes for any decorative elements or handles. If you have a specific pattern or stencil, place it on the clay and trace around it to ensure precision.
Consider the sizing of your brush holder to accommodate the brushes you intend to store. After cutting, lightly smooth the edges with a damp sponge to prevent any sharpness and to give your pieces a clean finish, preparing them for assembly in the subsequent steps.
Step 4: Assemble the Pieces
Using a scoring tool or fork, create lines and scratches on the edges of your clay pieces that will be joined together. This rough texture will help the clay adhere to itself when water is applied.
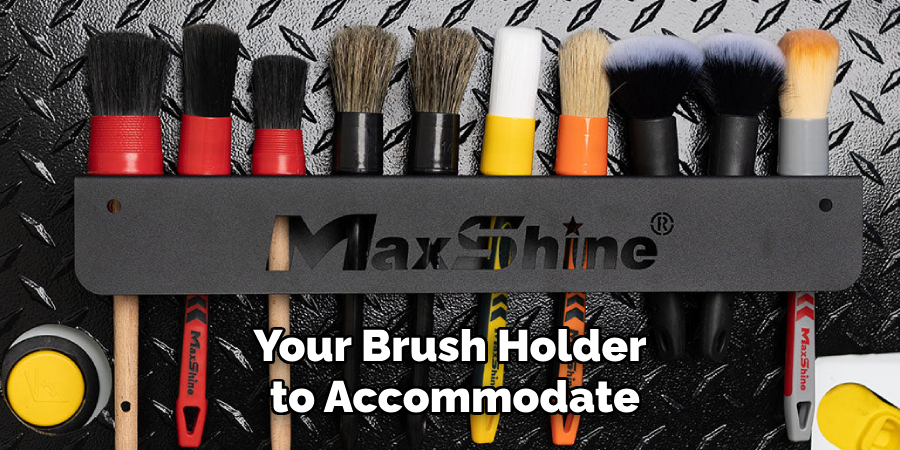
Apply slip (a mixture of water and clay) on both scored surfaces with a brush or your finger. Press the pieces together firmly, ensuring they are evenly aligned. Use your fingers or tools to smooth out any visible seams.
Step 5: Create Texture and Detailing
Once assembled, you can add textures and details to your brush holder using various pottery tools. You can carve designs into the surface, create imprints with stamps or fabric, or add texture by impressing patterns with tools like combs or forks. Be creative and experiment with different techniques to personalize your piece.
It is important to note that if using air-dry clay, this is the stage where you would let your piece dry completely before moving on to the next step.
Step 6: Allow the Clay to Dry
Let your brush holder dry completely before firing it in the kiln. This process can take several days, depending on the thickness of your clay and the humidity in your workspace. To prevent cracking, rotate and flip your piece regularly as it dries.
If using air-dry clay, allow it to sit for at least 24 hours before handling or painting it.
Step 7: Fire the Piece in a Kiln
If using ceramic clay, once your piece is completely dry, it is ready to be fired in a kiln. Follow the instructions on your chosen type of clay for firing temperatures and duration. Once fired, the colors of the glazes will become more vibrant and permanent, giving your brush holder a glossy finish.
You can choose to add multiple layers and colors of glazes to create a unique design for your brush holder.
Step 8: Add Final Touches
After firing and glazing, you can add any additional touches such as handles, additional decorative elements, or a final coat of clear glaze for extra shine. Once completed, let your piece dry completely before using it to ensure the durability of the clay and glazes.
Following these simple steps on how to make ceramic brush holders, you can create a one-of-a-kind ceramic brush holder that is not only functional but also adds a touch of handmade beauty to your workspace. Get creative and have fun making unique designs for yourself or as gifts for friends and family.
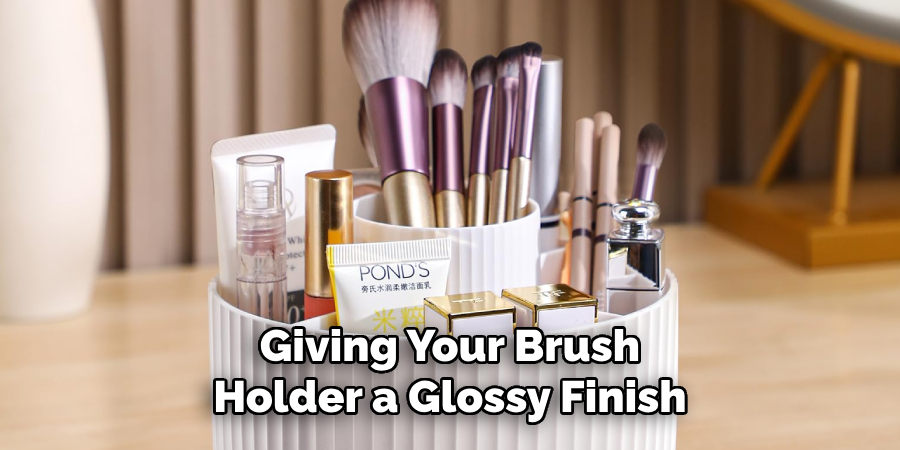
Additional Tips
- Keep a bowl of water nearby to keep your hands and tools moist while working with the clay.
- Be patient and take breaks when needed, as pottery is a slow and delicate process.
- Use reference images or sketches to guide you in creating your design.
- Experiment with different textures, shapes, and colors to make your brush holder truly unique.
- Don’t be afraid to make mistakes. Pottery is about trial and error, so embrace the learning process.
- Consider making multiple brush holders with different designs for a cohesive set in your workspace.
- Clean your tools and work surfaces after each use to maintain their longevity.
- Always follow safety precautions when using kilns or other equipment designed for pottery making.
- Have fun and let your creativity flow! Your ceramic brush holder is not just a functional item but also a piece of art that reflects your individual style and personality. Enjoy the process and be proud of your handmade creation.
Frequently Asked Questions
Q: Can I Use Any Type of Clay for Making a Brush Holder?
A: It is recommended to use ceramic or air-dry clay specifically designed for pottery as they have different properties and techniques for handling, firing, and glazing. You can experiment with other types of clay, but be aware that the results may vary.
Q: Can I Make a Brush Holder Without Using a Kiln?
A: Yes, you can use air-dry clay and follow the instructions on the packaging for drying and sealing the piece. Keep in mind that air-dry clay may not be as durable or have the same finish as kiln-fired ceramics.
Q: How Do I Care for My Ceramic Brush Holder?
A: To maintain the longevity of your ceramic brush holder, avoid putting it in direct sunlight or extreme temperatures. Clean it gently with a damp cloth when needed, and handle it with care to prevent any damage. With proper care, your handmade brush holder can last for many years to come.
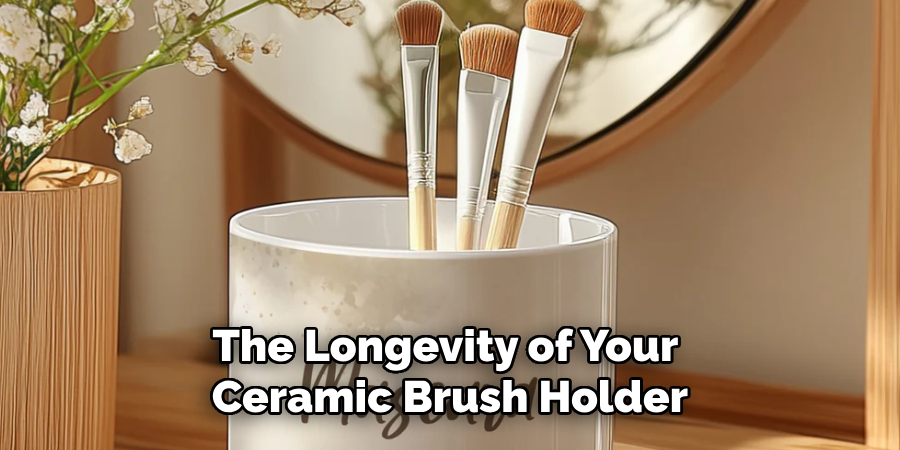
Conclusion
Creating a ceramic brush holder allows you to combine function with creativity and personalize your workspace. The process may take time and patience, but the end result is a beautiful handmade piece that will be both practical and aesthetically pleasing.
So why settle for a store-bought brush holder when you can create your own unique design? Give it a try and see the pride and satisfaction that comes with making something by hand. Thanks for readin gthis articl on how to make ceramic brush holders.
Professional Focus
Harry Ciotti is a highly skilled kiln operator with a sharp eye for detail and an in-depth understanding of the firing process. His expertise ensures that each ceramic piece reaches its full potential, perfectly balancing strength and beauty. Harry takes pride in overseeing the final stage of pottery creation, transforming raw clay into durable and stunning works of art.
About the Author
Harry Ciotti is a dedicated kiln operator and ceramic artist who brings passion and precision to every piece he fires. With a deep commitment to craftsmanship, Harry ensures that every ceramic creation is fired to perfection, from delicate vases to robust sculptures. He not only operates the kiln, but understands the unique needs of each piece, ensuring it reaches its full artistic potential. Through his work, Harry blends precision with artistry, making every firing a story of transformation.
Education History
University: California College of the Arts
Degree: Master of Fine Arts in Ceramics
Harry’s advanced education in ceramics has refined his technical skills, particularly in kiln operation, firing processes, and ceramic artistry. His educational background equips him to produce top-quality ceramic pieces that reflect both technical excellence and artistic expression.
Expertise:
- Kiln Operation and Firing Techniques
- Ceramics Creation (Functional and Artistic)
- Precision Craftsmanship
- Glazing and Texture Techniques
- Ceramic Artistry and Storytelling