Are you looking for a fun and creative activity? Making diy ceramic planters is a great way to express your creativity and have a functional piece of art.
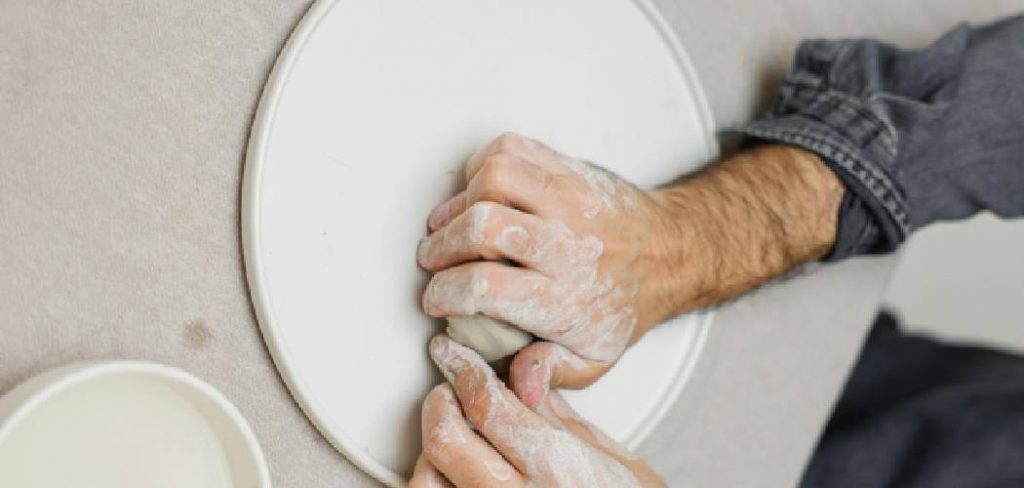
How to make a ceramic plate is a rewarding and creative process that combines craftsmanship and artistry. Whether you’re a beginner exploring pottery for the first time or an experienced ceramist, making your own plate allows you to design a unique and functional piece that reflects your personal style. This guide will walk you through the essential steps, from preparing the clay to firing and glazing, ensuring a durable and beautiful finished product.
With the right tools, patience, and a willingness to experiment, you’ll be able to craft a plate that is not only practical but also an actual work of art.
What Are the Benefits of Making a Ceramic Plate?
Before we dive into the steps, let’s explore some of the benefits of making a ceramic plate.
- Personal Expression: Crafting your plate allows you to express your individual style and creativity. You can experiment with different shapes, colors, and designs to create a truly unique piece.
- Therapeutic Activity: Working with clay can be a relaxing and meditative process. It allows you to disconnect from technology and focus on creating something tangible with your hands.
- Functional Art Piece: Ceramic plates are beautiful to look at and serve a practical purpose in everyday life. Whether for serving or display purposes, your handmade plate will add a special touch to any home.
- Sustainable Choice: Making your ceramic plate means you can avoid purchasing mass-produced and potentially environmentally damaging products. Plus, you can recycle and reuse excess clay, making it a more sustainable choice.
What Will You Need?
To get started on your ceramic plate-making journey, here are the essential materials you will need:
- Clay: This is the main material used to make your plate. Various types of clay are available, such as earthenware, stoneware, and porcelain. Each type has different properties that affect its durability and appearance, so research to find the best fit for your project.
- Pottery Wheel or Slab Roller: Depending on the design and size of your plate, you will need either a pottery wheel or a slab roller. The pottery wheel is used for throwing and shaping clay on a rotating wheel, while the slab roller is used for rolling out flat sheets of clay.
- Rolling Pin: If you use a slab roller, you will also need a rolling pin to flatten and smooth out the clay.
- Pottery Tools: These include trimming tools, carving tools, rib tools, and sponge tools that help shape and refine your plate’s design.
- Kiln: A kiln is essential for firing your ceramic plate at high temperatures to harden it and make it durable. If you don’t have access to a kiln, consider taking your plate to a local pottery studio or community center that offers firing services.
- Glaze: Glaze is what gives your plate its final color and finish. Various types of glazes are available, such as matte, glossy, and textured. Experiment with different combinations to achieve the desired effect for your plate.
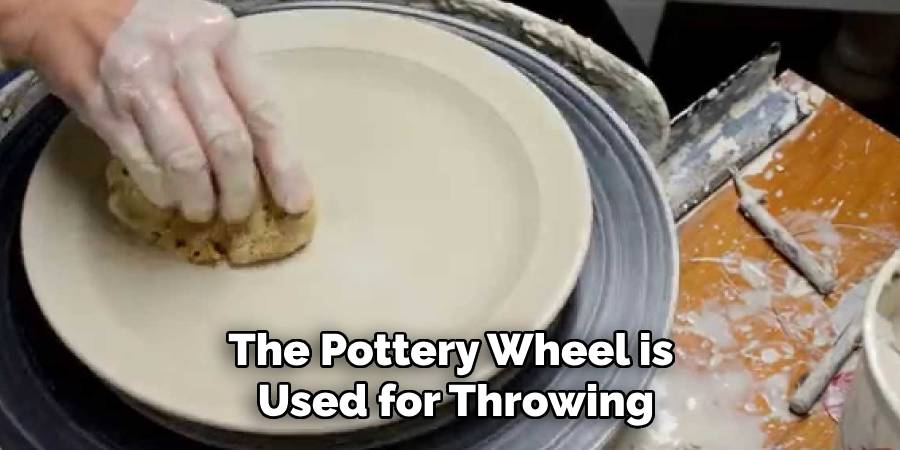
Once you have all the necessary materials, it’s time to start creating!
8 Easy Steps on How to Make a Ceramic Plate
Step 1: Prepare Your Clay
Begin by adequately preparing your clay to ensure it’s smooth and free of air bubbles. Start by wedging the clay, which involves kneading it thoroughly on a hard surface. This process helps remove air pockets that could cause cracking during firing and aligns the clay particles, making it more pliable and easier to work with. Use a wedging board if possible, preventing the clay from sticking to your work surface.
Once you’ve wedged your clay, divide it into a workable portion depending on the plate size you want to create. Cover any unused clay with plastic wrap or store it in an airtight container to keep it moist and prevent it from drying out. Proper preparation at this stage will lay the foundation for a successful and smooth crafting process.
Step 2: Roll Out the Clay
Take the prepared portion of your clay and roll it out evenly using a rolling pin or a slab roller. Ensure the thickness is consistent throughout, ideally around 1/4 inch thick for a standard plate. To prevent the clay from sticking to the surface or roller, use a clean canvas or another non-stick material beneath and on the clay while rolling. Take your time to achieve a smooth and even slab, as this will serve as the base for your ceramic plate.
Step 3: Cut Out the Plate Shape
Using a template or a circular object as a guide, cut out the desired shape of your plate from the rolled-out clay slab. A large bowl, plate, or compass can help ensure a perfectly round shape. Use a sharp knife or a specialized clay cutter to make clean, precise cuts. If you’d like to make a plate with a more unique design, feel free to experiment with other shapes such as squares or ovals. Carefully remove the excess clay around the shape and smooth the edges with your fingers or a damp sponge to ensure a refined finish.
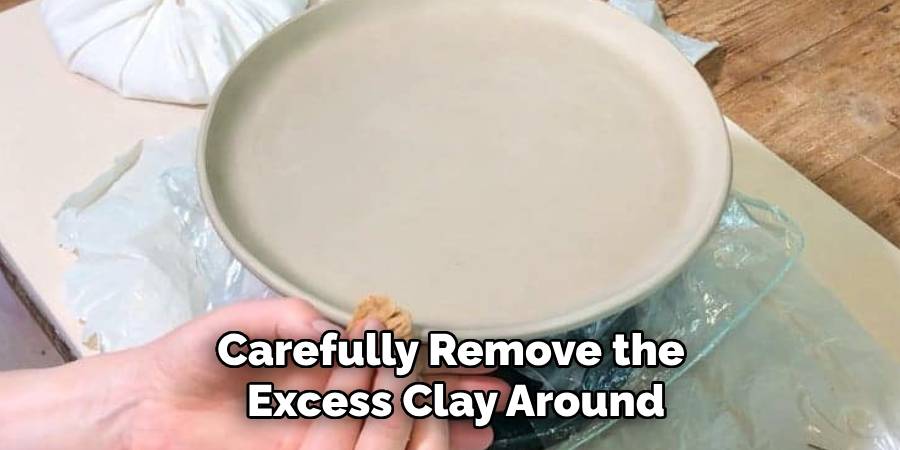
Step 4: Shape the Plate Edges
Once the basic shape of the plate has been cut out, you can start shaping the edges to give it a more refined and custom appearance. To create a slightly raised edge, gently pinch and lift the perimeter of the clay, working your way around the entire outline. Make sure to keep the height consistent for a uniform look.
Alternatively, you can use a wooden modeling tool or rib to smooth and curve the edges as desired. Consider adding subtle textures or patterns along the rim using stamps or other tools for creative designs. When satisfied with the plate’s shape, ensure all edges are smooth to prevent sharp areas after firing.
Step 5: Dry the Plate
After shaping the plate to your desired design, allowing the clay to dry thoroughly before moving on to the next stage is essential. Place the plate on a flat, dry surface, preferably covered with parchment or canvas to prevent sticking. Ensure the plate maintains its shape by ensuring the edges remain evenly supported while drying.
Depending on the thickness of the clay and environmental conditions, it may take a day or more for the plate to dry completely. To minimize cracking or warping, dry the plate slowly by placing it under a loose cover, such as a plastic sheet, to regulate the drying process. Once the plate is completely dry, it will be ready for the next step in the process.
Step 6: Bisque Firing
Once the plate is completely dry, it is time for the bisque firing. This initial firing process hardens the clay into a durable ceramic material, making it ready to accept glazes. Place the dried plate carefully into the kiln, ensuring it does not touch other pieces to avoid sticking.
Fire the kiln to the appropriate bisque temperature, typically between 1730°F and 1940°F (945°C to 1060°C), depending on the type of clay used. Allow the kiln to cool completely before removing the plate. After this step, the plate will have a porous surface that is ideal for glazing.
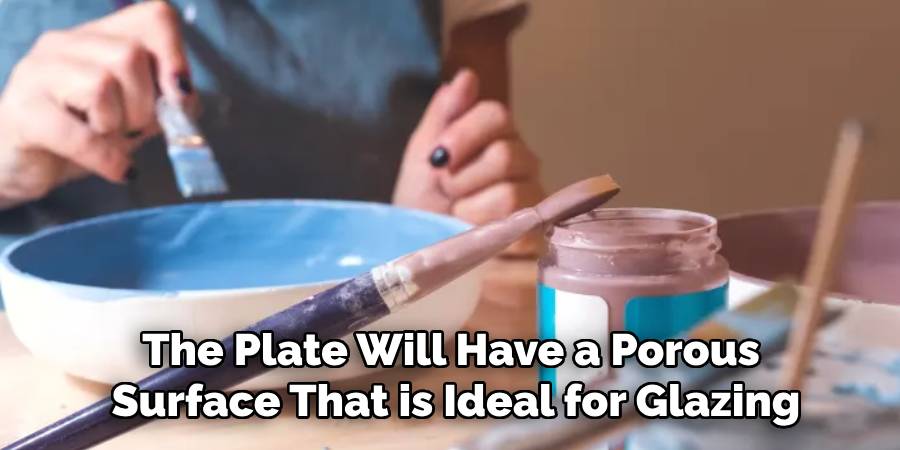
Step 7: Glazing
With the plate bisque-fired and ready, the next step is glazing. Glazing gives the finished plate its color, texture, and protective coating. Choose a glaze that complements your desired aesthetic and functionality. Dip, brush, or spray the glaze onto the plate, ensuring an even application. Avoid excessive glazing on the bottom of the plate, as this can cause it to stick to the kiln shelf during the subsequent firing. Allow the glaze to dry completely before the final firing step.
Step 8: Final Firing
After the glaze has dried, the plate is ready for the final firing, often called the glaze firing. Carefully place the glazed plate into the kiln, ensuring it does not come into contact with other pieces to avoid damage. Fire the kiln to the appropriate glaze temperature, which typically ranges between 1820°F and 2300°F (993°C to 1260°C), depending on the type of glaze and clay used.
This process allows the glaze to melt and fuse to the surface of the plate, creating a smooth and durable finish. Once the firing is complete, the kiln will cool completely before the plate is removed. The result is a beautifully crafted, functional ceramic plate ready for use or display.
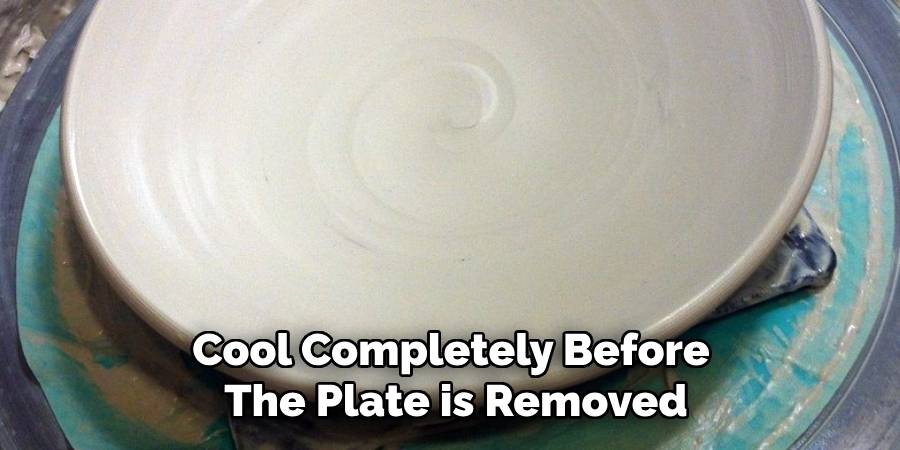
By following these steps and taking time, you can create a unique ceramic plate showcasing your creativity and craftsmanship.
Conclusion
How to make a ceramic plate is a rewarding process that combines patience, creativity, and technical skill.
You can produce a stunning and functional piece of art by carefully following each step—from preparing the clay and shaping the plate to bisque firing, glazing, and final firing. Every decision, from the design to the glaze selection, allows you to express your style and bring your vision to life.
Making ceramic plates can become a fulfilling and enjoyable craft with practice and dedication, resulting in beautiful, handmade creations to cherish or share with others.
Professional Focus
Harry Ciotti is a highly skilled kiln operator with a sharp eye for detail and an in-depth understanding of the firing process. His expertise ensures that each ceramic piece reaches its full potential, perfectly balancing strength and beauty. Harry takes pride in overseeing the final stage of pottery creation, transforming raw clay into durable and stunning works of art.
About the Author
Harry Ciotti is a dedicated kiln operator and ceramic artist who brings passion and precision to every piece he fires. With a deep commitment to craftsmanship, Harry ensures that every ceramic creation is fired to perfection, from delicate vases to robust sculptures. He not only operates the kiln, but understands the unique needs of each piece, ensuring it reaches its full artistic potential. Through his work, Harry blends precision with artistry, making every firing a story of transformation.
Education History
University: California College of the Arts
Degree: Master of Fine Arts in Ceramics
Harry’s advanced education in ceramics has refined his technical skills, particularly in kiln operation, firing processes, and ceramic artistry. His educational background equips him to produce top-quality ceramic pieces that reflect both technical excellence and artistic expression.
Expertise:
- Kiln Operation and Firing Techniques
- Ceramics Creation (Functional and Artistic)
- Precision Craftsmanship
- Glazing and Texture Techniques
- Ceramic Artistry and Storytelling