Are you interested in creating colorful and unique jewelry or decorations for your home? Look no further than polymer clay!
Polymer clay has become a favorite medium among artists and hobbyists alike due to its versatility and ease of use. Properly preparing polymer clay before diving into a creative project is essential for achieving the best results. This process involves conditioning the clay to make it soft and pliable, ensuring an even blend of colors and preventing cracks or breaks during baking.
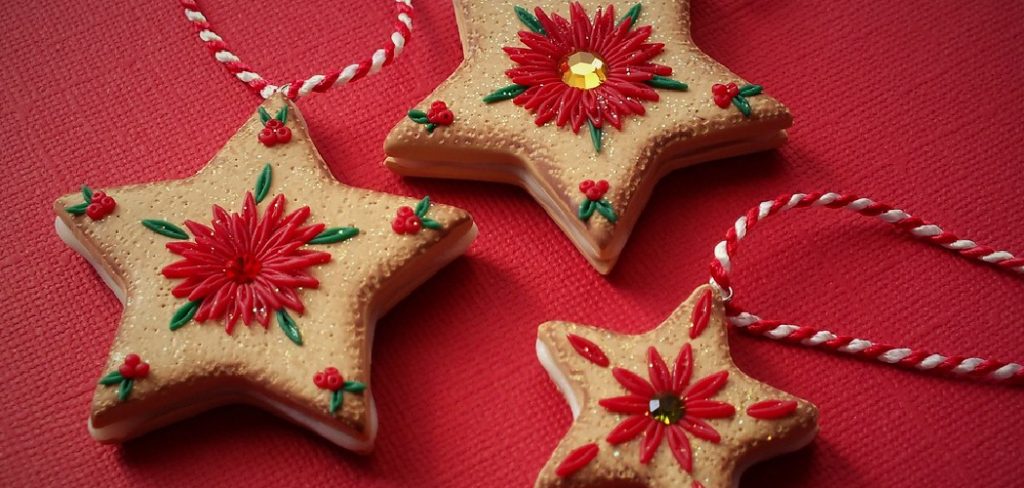
By understanding the steps on how to prepare polymer clay, you can ensure that your creations are not only visually appealing but also durable. Whether you’re crafting jewelry, figurines, or home decor, taking the time to prepare your clay will enhance your crafting experience and elevate your finished pieces.
What Will You Need?
To prepare polymer clay, you’ll need the following materials:
- Polymer clay in your desired colors
- A flat surface (such as a ceramic tile or glass cutting board)
- A pasta machine or rolling pin
- Wax paper or parchment paper
- An acrylic roller or brayer
- Craft knife or blade for cutting
- Your hands!
10 Easy Steps on How to Prepare Polymer Clay
Step 1: Condition the Clay
Conditioning polymer clay is a crucial step that involves warming and softening it to make it more malleable. Begin by cutting the clay into smaller pieces if it’s a large block—this can make the conditioning process more manageable. Using your hands, knead the clay by pressing and folding it repeatedly.
This manual heat helps to soften the clay, making it easier to work with. If you have a pasta machine, pass the clay through it several times, gradually reducing the thickness setting. This softens the clay and helps evenly distribute the plasticizers within it, reducing the likelihood of cracking or breaking during baking. Continue conditioning until the clay is smooth and can be easily stretched without cracking, ensuring it’s ready for your creative projects.
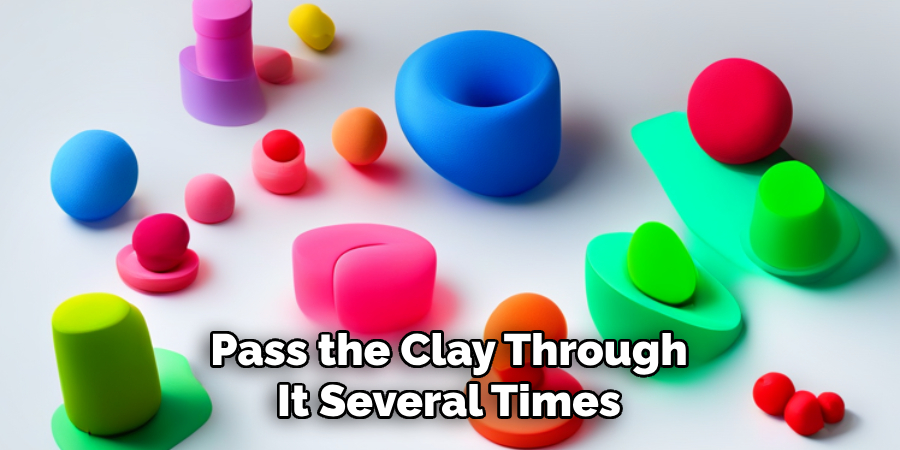
Step 2: Flatten and Shape the Clay
After conditioning, flatten the clay into a manageable shape. Lay the conditioned clay on your flat surface and roll it out evenly using an acrylic roller or brayer. This helps create a uniform thickness. If you desire a perfectly even thickness, use guide wires or rolling pin rings to maintain consistency.
Roll the clay from the center outward to avoid creating thin edges, flipping it occasionally to ensure even flattening. Shaping the clay at this stage makes cutting or molding your desired form for your project easier.
Step 3: Cut the Clay
Once your clay is evenly flattened and shaped, it’s time to cut it according to your project’s needs. Use a craft knife or blade to slice the clay into the desired shapes or sizes. Be precise and deliberate with your cuts to ensure clean edges; a straight blade works well for straight lines, while a curved blade can be used for more intricate designs.
If you are creating multiple pieces that should be the same size, consider using a clay cutter or template to maintain uniformity. The cutting stage is important for setting the foundation of your final design, so take your time to achieve the exact shapes you envision for your creations.
Step 4: Combine Colors or Textures
If your project involves blending different colors or incorporating textures, this is the perfect time to do so. Start by arranging the various colors of conditioned clay near each other. Gently press them together and roll them through the pasta machine or with the acrylic roller, ensuring the edges merge seamlessly.
For marbled effects, twist and fold the colors before rolling them out. To add texture, press textured mats or household items like leaves or fabric onto the surface of the clay. Experimenting with colors and textures allows you to add a unique flair to your clay creations, making each piece unique.
Step 5: Assemble and Arrange Pieces
Once you have cut and combined colors or textures, it’s time to assemble the individual pieces. Lay out all the components of your design on your work surface. Carefully arrange them, testing different configurations if necessary, to achieve the desired appearance for your project.
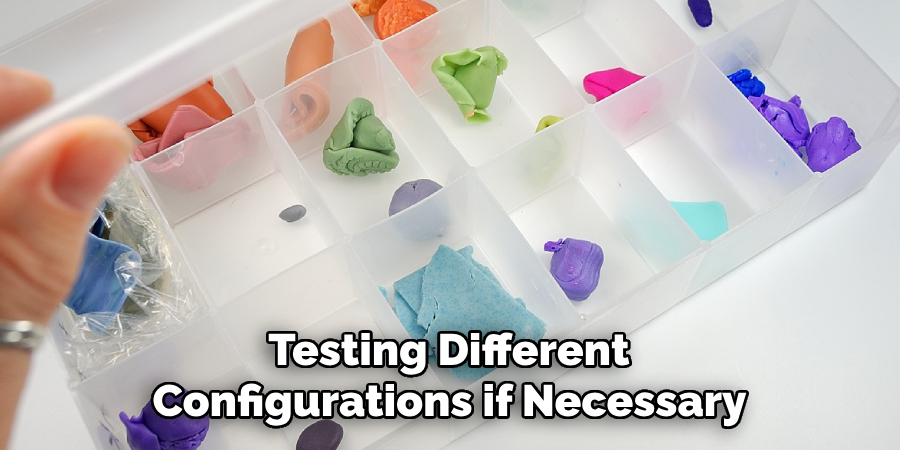
If you’re crafting a piece that requires overlapping elements, layer the pieces deliberately, pressing gently to ensure they adhere to each other. As you assemble, pay attention to details like the alignment and proportion of the elements to ensure your creation looks balanced and cohesive.
Step 6: Remove Air Bubbles
Before proceeding to the baking stage, it’s essential to eliminate any trapped air bubbles from your clay creation. Air bubbles can cause cracks or imperfections during baking. To remove them, gently press over the surface of your clay using your fingers or a flat tool, feeling for any raised areas.
If you find a bubble, use a needle tool to carefully pierce it, then smooth over the area with an acrylic roller or your fingers to ensure a seamless surface. This precaution helps maintain the integrity of your artwork, resulting in a smooth, professional-looking finish.
Step 7: Bake the Clay
Once you have eliminated air bubbles, your project is ready for baking. Preheat your oven to the temperature specified on your clay’s packaging—typically around 265°F to 275°F (129°C to 135°C). Place your clay pieces on a baking sheet lined with parchment or a ceramic tile to ensure even heat distribution.
Bake the clay as recommended, usually about 15-30 minutes per 1/4 inch (6 mm) of thickness. Keep an eye on your items throughout baking to prevent overbaking, which can cause the clay to darken or burn. Once baked, allow the clay to cool completely before handling or polishing it, ensuring durability and strength in your finished piece.
Step 8: Sand and Polish the Clay
After the clay has wholly cooled from baking, it’s time to sand and polish your creation for a smooth finish. Use fine-grit sandpaper to sand the surface, removing imperfections or rough edges gently. Start with a coarser grit and gradually move to finer grits for a polished look.
Be careful not to sand too aggressively, which can damage the surface. After sanding, you can polish the clay using a soft cloth or a buffing wheel to bring out a nice sheen. Polishing adds professionalism to your piece, making your handmade creation look refined and complete.
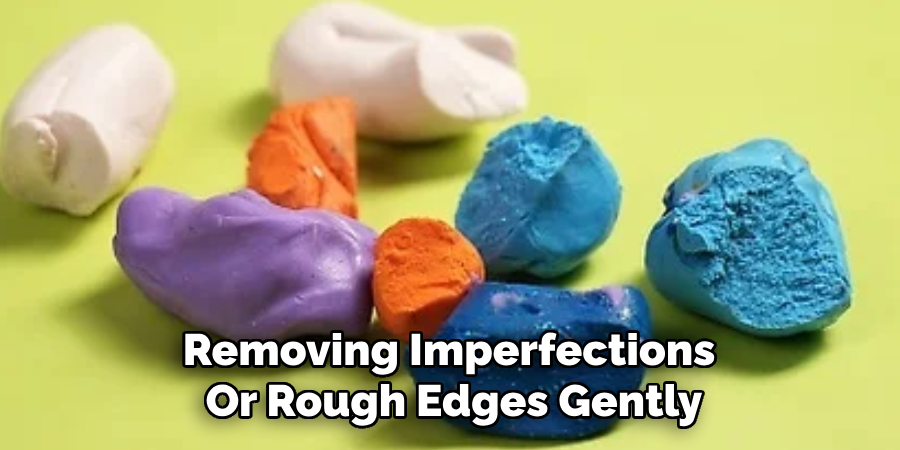
Step 9: Finishing Touches
With the sanding and polishing complete, it’s time to add any final touches to your clay project. This could include adding details such as painting, glazing, or applying metallic leaves for a decorative finish. If you’re using paints or glazes, ensure they are compatible with polymer clay. Use a small brush to apply details or add depth with shading.
Allow any additional layers to dry thoroughly. For pieces that require assembly or attaching findings, like jewelry components, consider using strong adhesive or drilling small holes for connectors. These final touches personalize your project and elevate it to the next level of craftsmanship.
Step 10: Seal and Protect
Apply a sealant for protection to ensure your clay project remains beautiful and durable. Choose a suitable sealant that complements the finish of your clay piece, such as a glossy or matte varnish. Apply the sealant evenly using a brush, covering all surfaces, including any intricate details or assembled components. This protective layer will help safeguard your creation from moisture, dust, and general wear, enhancing longevity.
Allow the sealant to dry completely per the manufacturer’s instructions before handling your piece. Sealing your clay projects not only preserves their aesthetic appeal but also adds an extra layer of durability, ensuring your handcrafted masterpiece stands the test of time.
Following these ten steps, you can create beautiful, professional-looking polymer clay projects that showcase your creativity and talent.
5 Things You Should Avoid
- Over-Conditioning the Clay: While conditioning is essential to make the clay pliable, overdoing it can result in a sticky, difficult-to-manage consistency. Aim for a balance where the clay is soft yet maintains its shape.
- Using the Wrong Tools: Avoid using metal tools that can potentially react with the clay. Instead, opt for plastic tools explicitly designed for polymer clay to ensure the best results without contamination.
- Exposing to Dust and Debris: Make sure your workspace is clean, as polymer clay readily picks up lint, dust, and other small particles. These can become embedded in your work and affect the final appearance.
- Neglecting Temperature Control: Avoid preparing your clay near heat sources or direct sunlight, which can start the curing process prematurely and alter the texture.
- Ignoring Proper Storage: Never store clay in direct sunlight or in conditions that expose it to extreme temperatures, as they can harden or melt your materials. Use airtight containers to keep your polymer clay safe and ready for future use.
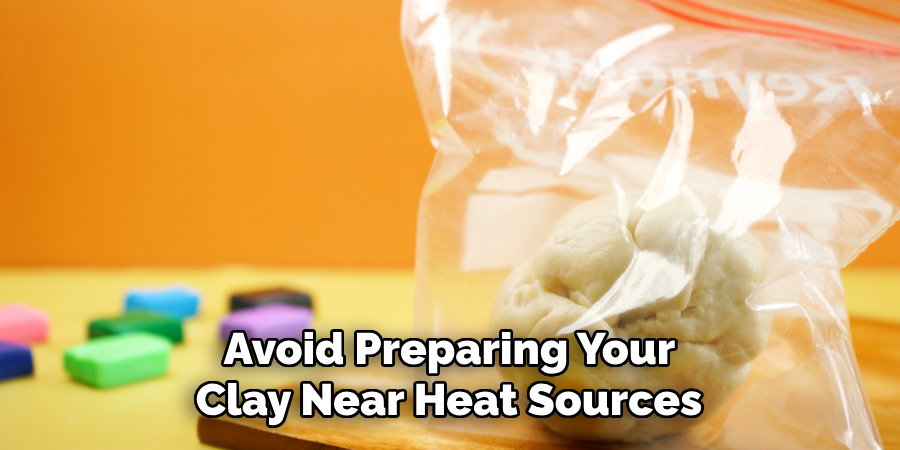
Conclusion
In conclusion, properly preparing polymer clay is crucial for achieving high-quality final results in your projects.
Condition the clay just enough to reach the desired softness without making it overly sticky. Use appropriate tools to prevent contamination and maintain a clean workspace to avoid unwanted debris. Pay attention to temperature control to prevent premature curing, and always store your clay in suitable environments to preserve its usability.
Hopefully, the article on how to prepare polymer clay has provided you with valuable information and tips to help you get started on your polymer clay journey. With practice and experimentation, you will discover your own techniques for preparing and working with this versatile material.
Professional Focus
Toby Rede, a professional potter, combines artistic expression with functionality in his ceramic creations. His work blends natural textures, modern forms, and sustainable materials, making him a standout voice in the pottery world focused on intentional craftsmanship.
About the Author
Toby Rede, a dedicated potter and blogger, shares his insights on functional and artistic ceramics, drawing inspiration from sustainable gardening and nature. Based in his studio, he blends craftsmanship with everyday life, encouraging others to incorporate handmade pottery into their homes for both beauty and utility.
Education History
University: Alfred University
Degree: Associate Degree in Ceramic Technology
Toby’s education laid the foundation for his technical expertise, equipping him with the skills necessary to create pottery that merges functionality and aesthetic appeal.
Expertise:
- Pottery Creation
- Ceramic Techniques (Texture, Glazing, Sustainable Materials)
- Functional Art and Design
- Craftsmanship Philosophy
- Blogging on Handmade Pottery and Everyday Life